液壓驅動與伺服驅動平齒機的能耗與效率對比是制造業設備選型的重要考量因素。從能耗角度看,液壓系統通常存在較高的能量損耗。傳統液壓驅動需通過電機帶動液壓泵產生高壓油液,能量需經歷"電能-機械能-液壓能-機械能"多級轉換,綜合效率通常低于40%。尤其在待機或低速運行時,溢流閥持續泄壓造成的空載損耗顯著,能耗可占全天運行的30%以上。而伺服驅動采用閉環控制系統,電機僅在實際工作時消耗電能,能量轉換效率可達85%-95%。其待機能耗近乎為零,整體能耗較液壓系統降低40%-60%。
效率方面,伺服驅動優勢更為突出。伺服系統響應速度可達毫秒級,加減速時間比液壓系統縮短50%以上,特別適用于高頻次啟停的加工場景。定位精度方面,伺服驅動可實現±0.01mm的重復定位精度,遠超液壓系統的±0.1mm水平。在加工效率上,伺服驅動平齒機的換刀時間可縮短至液壓設備的1/3,且通過動態扭矩補償功能,能保持切削過程的恒定功率輸出。而液壓系統受油溫變化影響,長時間運行易出現壓力波動,導致加工效率下降5%-8%。
但液壓系統在超重載、低速大扭矩場景仍具優勢,其瞬時過載能力可達額定值的3倍,適合特大型齒輪加工。伺服驅動雖初期投資高15%-20%,但通過節能改造通常可在2-3年收回成本。隨著永磁同步電機和碳化硅功率器件的應用,新型伺服系統的能效比已突破90%,正在快速替代傳統液壓設備,特別是在中小型精密齒輪加工領域。未來趨勢顯示,伺服驅動在能耗、效率、智能化方面的綜合優勢將主導平齒機技術升級方向。
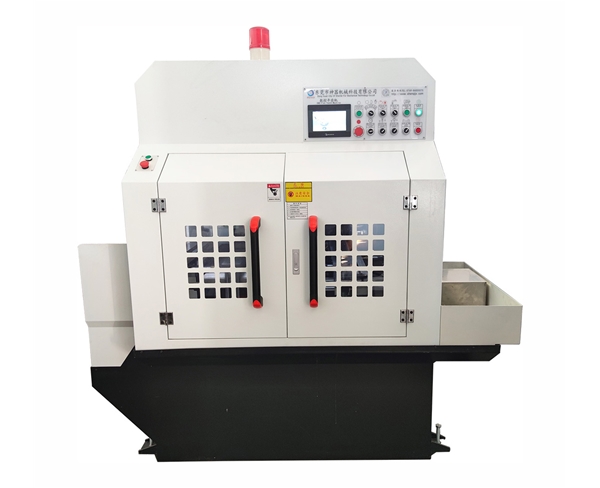